CORDOVAN - Dyeing section
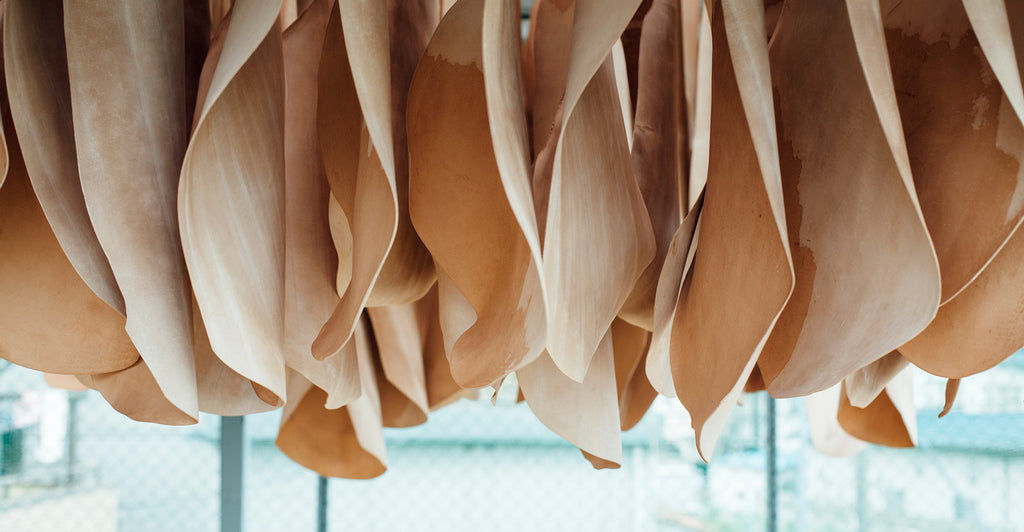

CORDOVAN — Dyeing sectionWater dyeing passed down from generation to generation

Cordovan featuring a natural texture
GANZO's cordovan is tanned and finished using a water-dyeing process called aniline dyeing. GANZO's cordovan is finished and dyed by the leather processing company LEDER OGAWA, where their unique water-dyeing method was born from the research of their founder who became fascinated by the dyeing of cordovan when he was a teenager. Carrying on the tradition of their founder who pioneered dyeing, 50 years since their establishment, the company produces cordovan with a natural texture using a unique dyeing method that allows water-based dye to soak into the leather to make the most of the leather's original surface. The result is characterized by its tactile matte texture, unique transparency, and gloss.
The main processes to finishing
-
Greasing
The greasing process involves stretching the leather using a special recipe of oils that easily soaks into the cordovan. The excess oil is squeezed out with a tool called a slicker after it has penetrated into the leather. Stretching out the leather at this time makes it hard and sturdy. This is an important process because if the leather is soft, it will not produce a clear luster after glazing is applied.
-
Cutting
After the leather is allowed to dry naturally, the cordovan layer, which is a dense fiber inner layer of the hide about 1 mm thick, is carved out. This cordovan layer is protected by the hard outer skin, and the fibers are fine and strong. The craftsman exposes the cordovan from the underside of the leather without destroying the fibers. If the leather surface is scratched, it cannot be redone, so great care must be taken when cutting out the cordovan.
-
Glazing
The surface of the leather is polished with a leather glazing machine, where a roller with raw agate attached to the end of the machine is used to apply pressure, and the heat from the friction causes the moisture to evaporate. This polishing process creates a natural luster, and is directly related to the gloss of aniline dyed cordovan. It does not apply a glossy finish, but rather allows the natural unevenness of the leather's original color, as well as the fibers themselves, to come to the surface as a gloss.
To the water dyeing process
After the glazing finish, it's on to the process of water dyeing. Unlike normal water dyeing, this process is called aniline dyeing, where only one side of the leather is subjected to the water dyeing process. After this process, the leather processing and dyeing process is complete.

Points of specialization
The artisans at LEDER OGAWA are particular about the shine and feel of their products. The more you use them, the more they mesh to your hands, and you can enjoy the changes over time, five years from now or even decades into the future. The key point is that the longer they're used, the more the leather's original expression gradually comes out. It is difficult to mass-produce, as cordovan is manufactured through many work processes spanning many phases.
The appeal of water dyeing
Ordinary water dyeing is a process in which the dye is dissolved in water and the color is absorbed into the entirety of the leather. By contrast, the aniline dyeing developed by LEDER OGAWA is a dyeing method in which soluble dyes are applied to only one side of the leather. With this method, the surface pattern of the leather remains visible.
Creator's mindset
LEDER OGAWA's water-dyeing method is an inherited technique that has been handed down from the previous generation and cannot be reproduced anywhere else. Those who are familiar with cordovan products, and even those who have never seen cordovan before, will be impressed by the beautiful translucent luster of the finished cordovan and its smooth touch. Our cordovan series has been made possible by the insatiable ambition, passion and persistence of its original creators, evolving and handed down to the present day.
